Walkaround du Rafale
Le Rafale en détail (plans en écorchés)
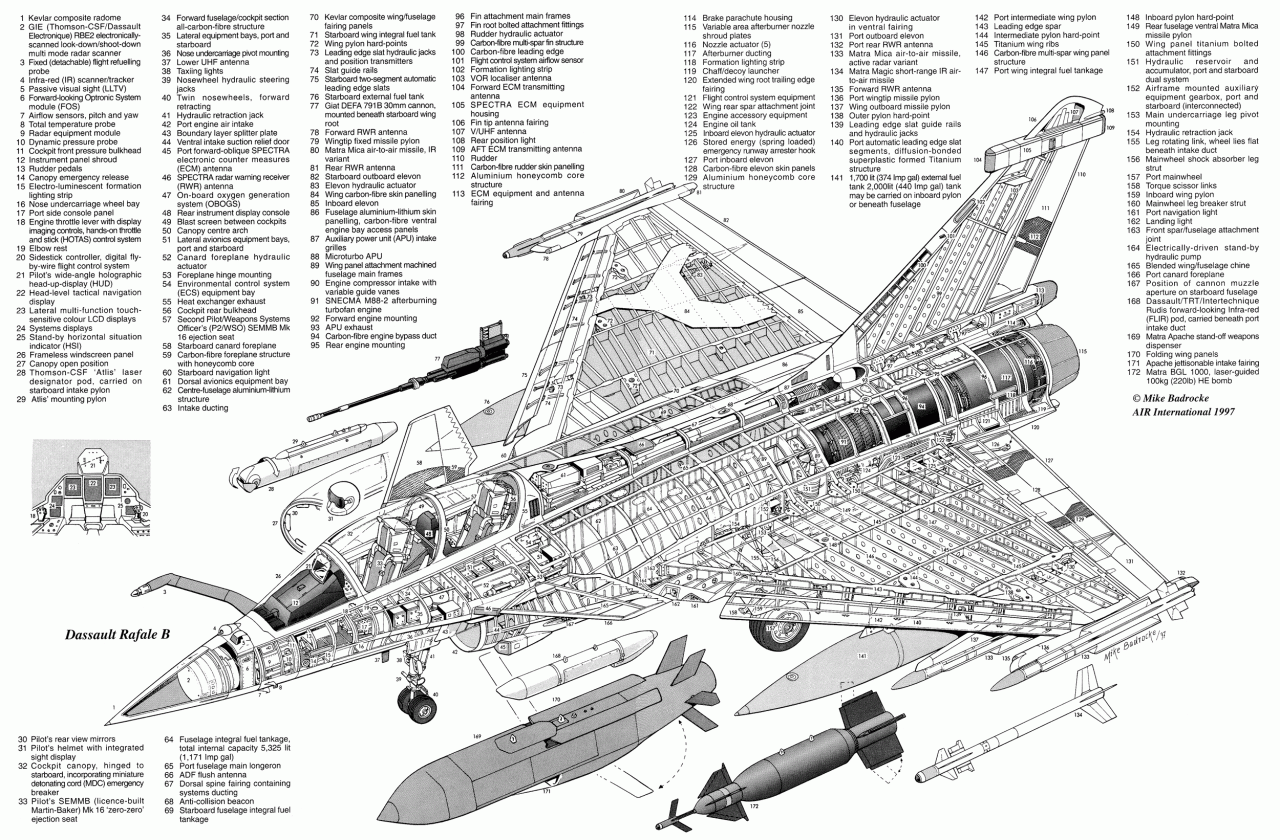
Plan en « écorché » d’un Rafale M
Les antennes de communication du Rafale
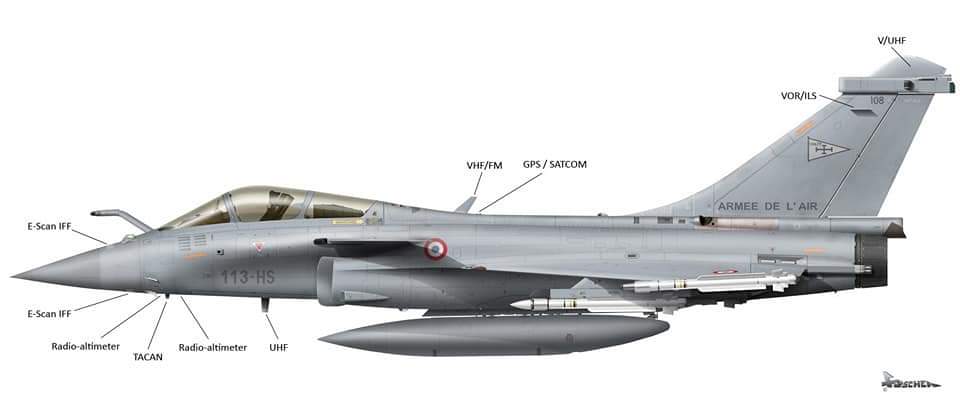
75% de matériaux composites composent le Rafale
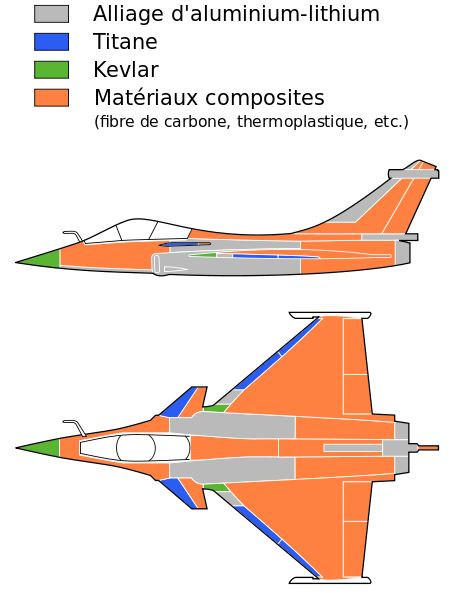
Les pièces doivent être les plus légères possible. Exemple le plus spectaculaire : les quatre panneaux de voilure du Rafale. Ces pièces sont réalisées d’un seul tenant par une machine à napper qui dépose les lés de tissu pré-imprégné par couches successives. Elles sont ensuite polymérisées sous vide en autoclave (4 m de diamètre et 9 m de long pour le plus gros). 75 % de la surface « mouillée » du Rafale est en matériaux composites. Ils représentent 1000 kg, soit 30 % de la masse de la cellule.
Le même principe, qui consiste à fabriquer le matériau en même temps que la pièce, s’applique également aux éléments de forme complexe réalisés par drapage manuel : pointe avant des Falcon en fibre d’aramide et gouvernes de Rafale en sandwich nid d’abeille.
Pour plus de précision, des projecteurs lasers sont notamment exploités pour optimiser le positionnement des couches et tracer les contours des plis.
Remarques :
- Le carbone a une densité de 1, 6 contre 2,8 pour l’aluminium avec une résistance supérieure.
- En terme de coût : de l’ordre de 250 € le kilo de carbone, contre 6 €/kg pour l’aluminium.
(article janvier 2007 – UIMM)
Un traitement des métallisations apporte une protection aux agressions IEMN (impulsion électromagnétique nucléaire), foudre et champs forts.
Le train d’atterrissage du Rafale « Marine »
Son fabriquant est Safran Landing Systems (Ex Messier Bugatti).
Il permet une accélération de 0 à 240 km/h en 3 secondes et des résistances de 90 à 100 tonnes.
Pour la version marine, le train avant a la capacité de restituer l’énergie qu’il a emmagasiné lors de son enfoncement initial provoqué par l’effort de traction de la catapulte. Après le catapultage, l’amortisseur est reconfiguré automatiquement pour permettre le meilleur amortissement possible en vue de l’appontage.
Lors du catapultage :
- La barre de traction située sur le train avant est placée dans le sabot de la catapulte.
- Un brin à casser retient alors le train, le hold back, taré à 35 tonnes.
- La pression augmente dans la catapulte et les réacteurs poussés à fond.
- Le brin casse en atteignant 35 tonnes de traction.
- Le train n’étant alors plus soumis à l’effort de traction, il restitue son énergie et provoque alors une accélération verticale favorable à l’envol.
De 0 à 300 km/h en 3 secondes
En définitive, les sorties de catapultes varient de 140 à plus de 170 kts selon les emports de charges et se réalisent sur à peine 75 mètres (contre 90 mètres sur les porte-avions américains).
Les atterrisseurs du Rafale M (version Marine) sont considérés comme le système le plus avancé disponible sur un avion embarqué à bord d’un porte-avions. Les trains avant et principaux ont été renforcés afin de répondre aux conditions difficiles d’atterrissage et de décollage que rencontre ce type d’appareil. Cette version renforcée est capable d’absorber une énergie verticale d’atterrissage correspondant à une vitesse de 6,5 mètres par seconde. Le train avant du Rafale M intègre la barre de catapultage (et son système opérationnel), et la technologie « jump strut » fournissant une poussée complémentaire lors du décollage.
Un des avantages de cet atterrisseur est sa manœuvrabilité au sol avec une roue qui peut être orientée sur 360°et pilotée sur +/-75°.
Sur la partie haute du train avant, on observe un boîtier disposant de 3 lampes (vert, ambre et rouge). Il s’agit d’une information visuelle destinée à l’officier d’appontage, relative à l’incidence de l’avion. En revanche, à l’opposé, on y trouve un phare de roulage.
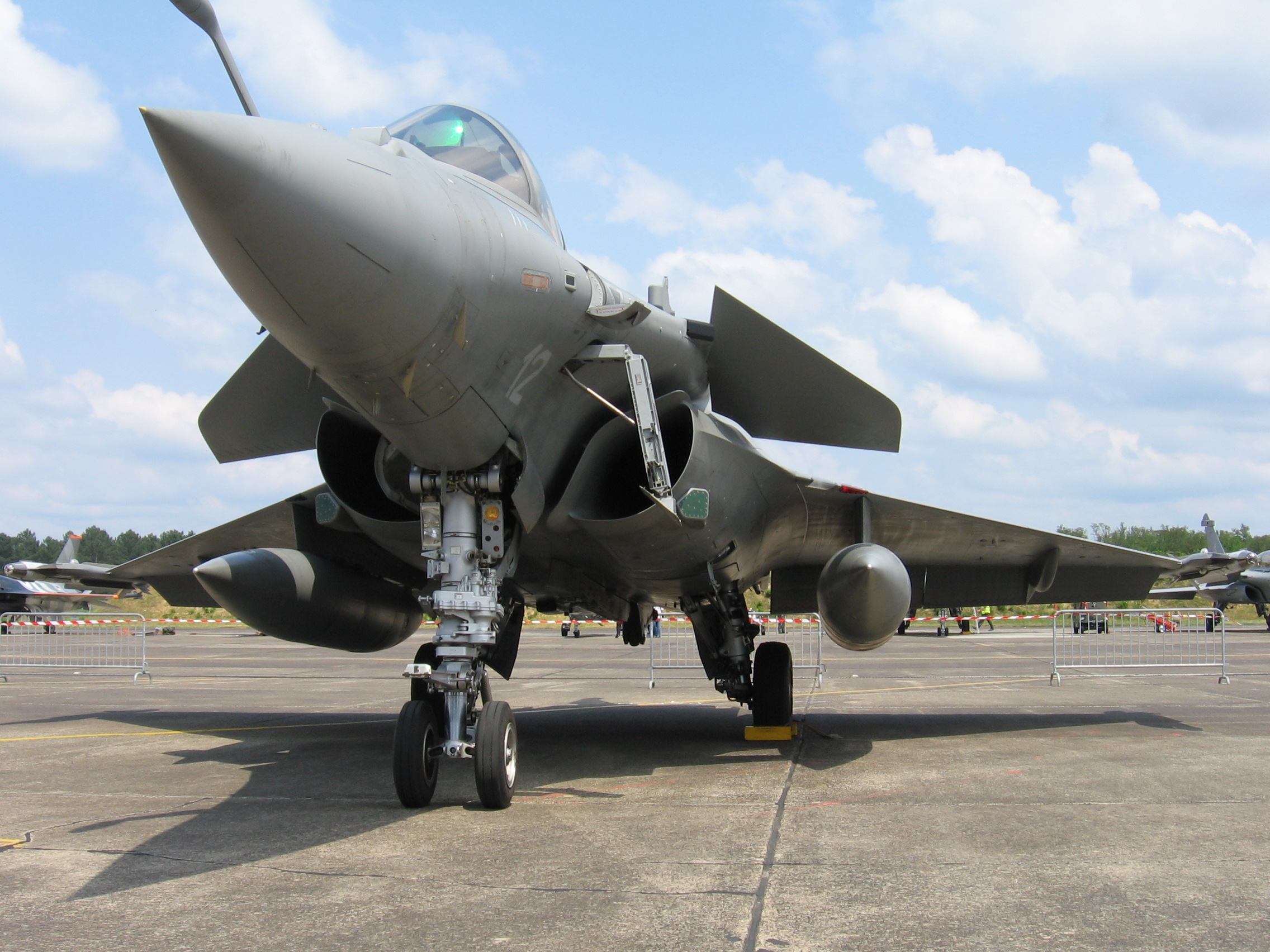
Le train d’atterrissage du Rafale « Air »

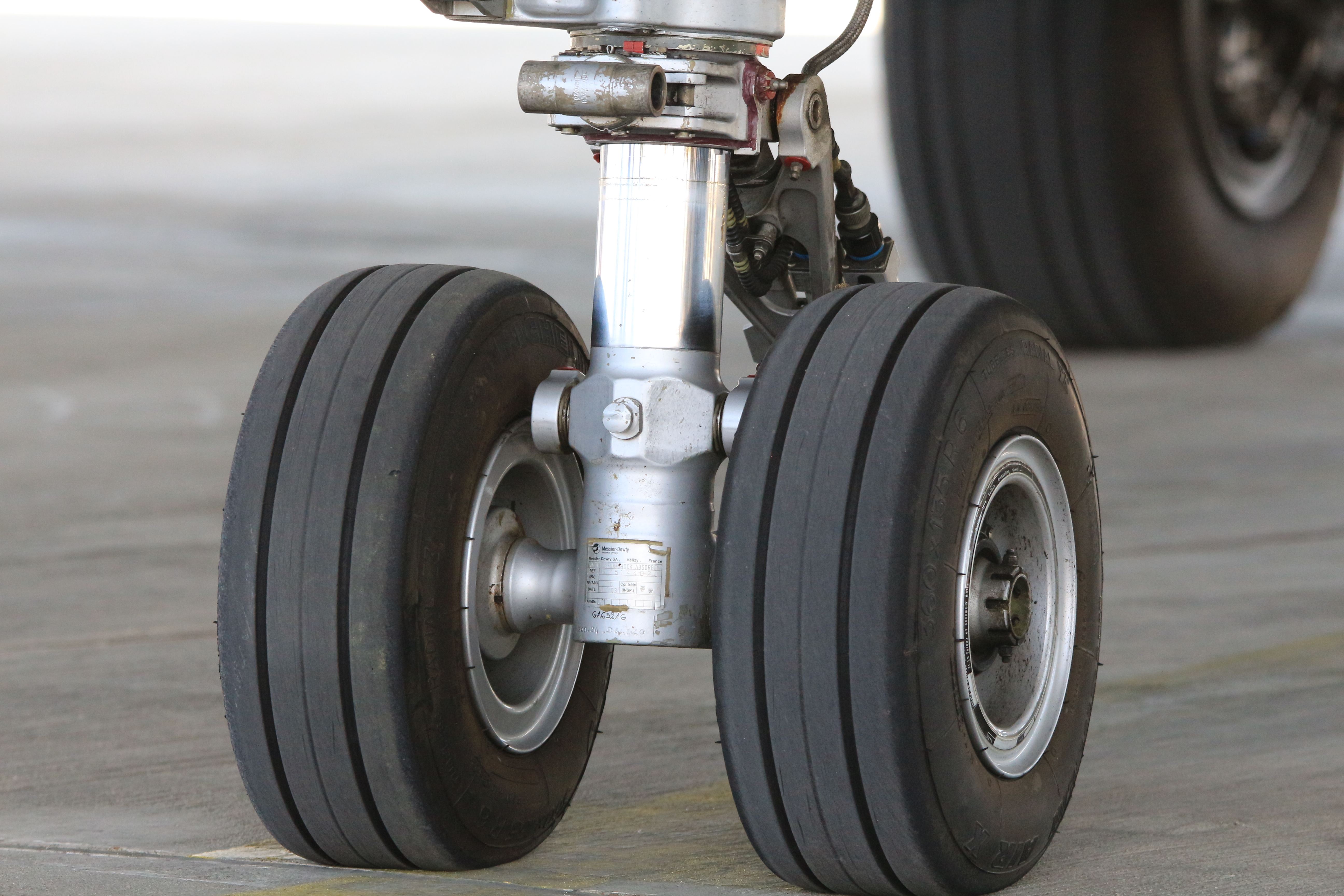

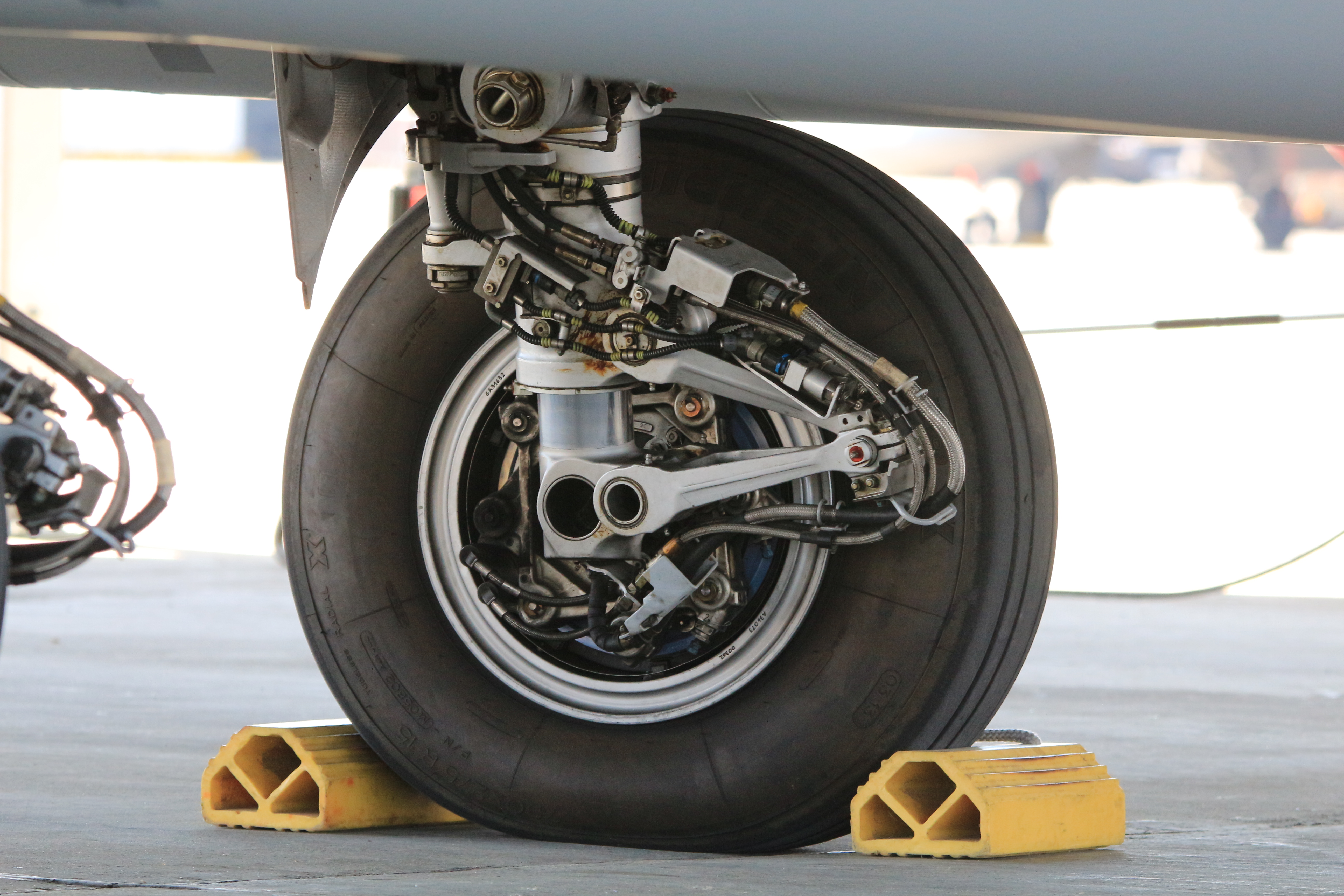



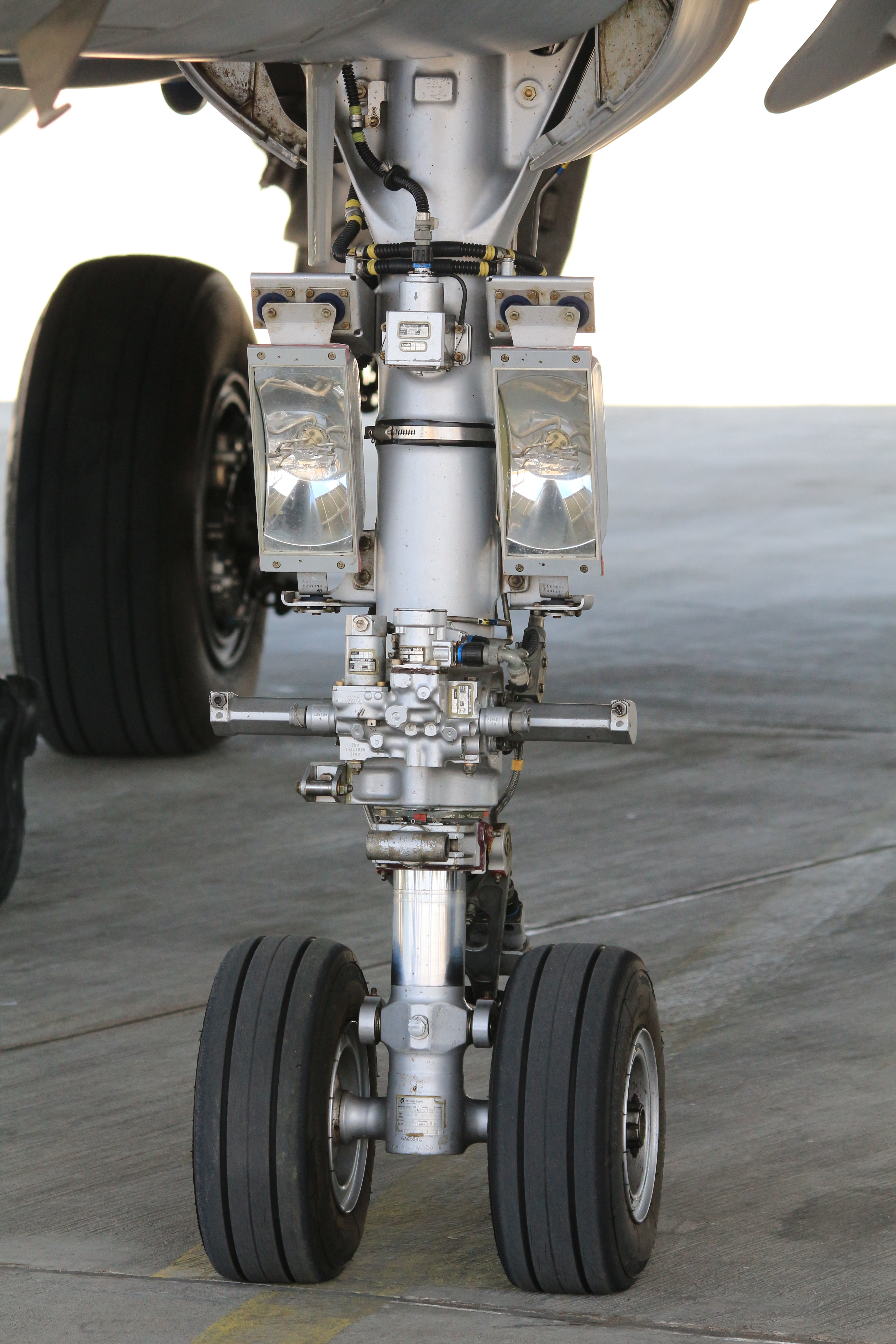

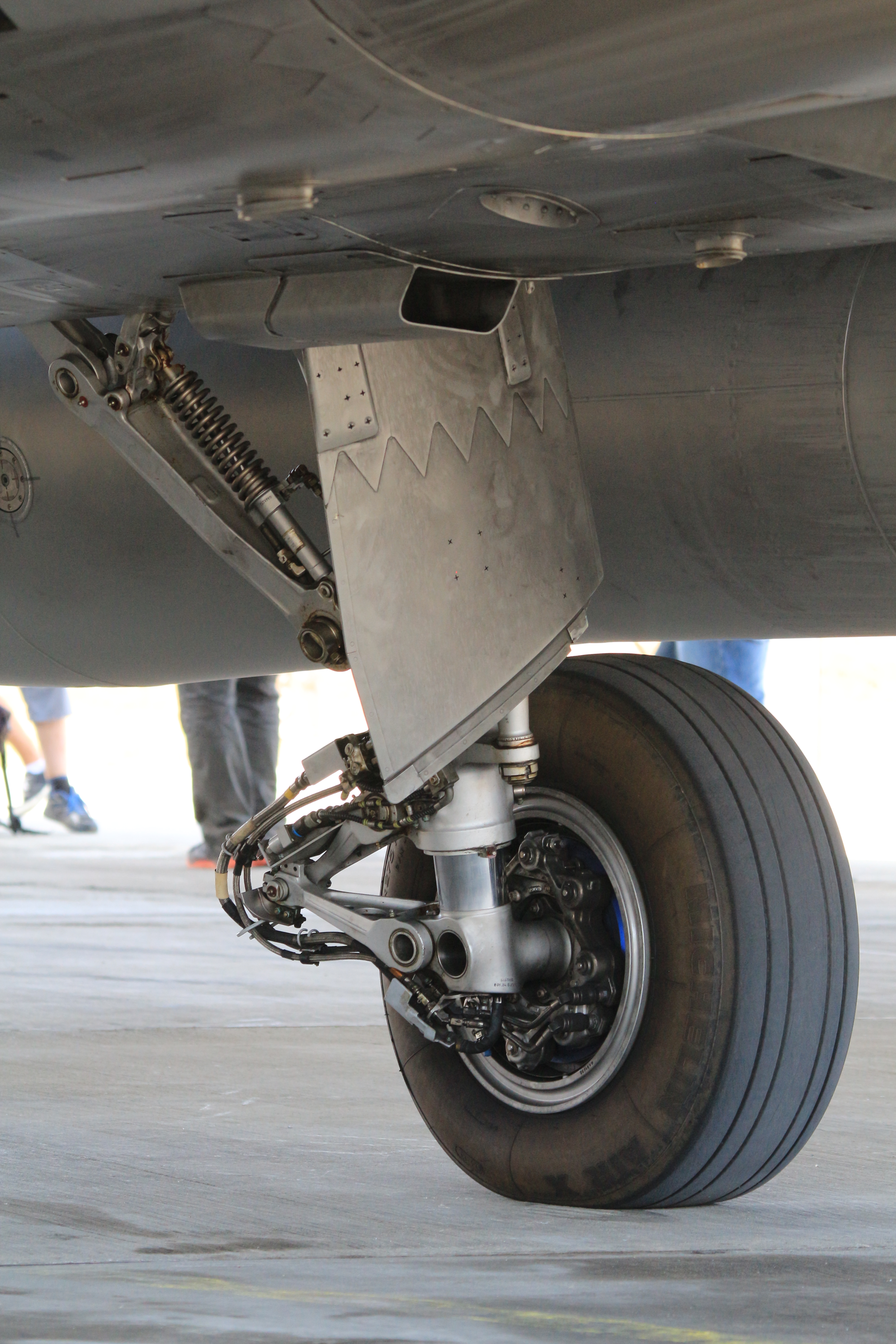

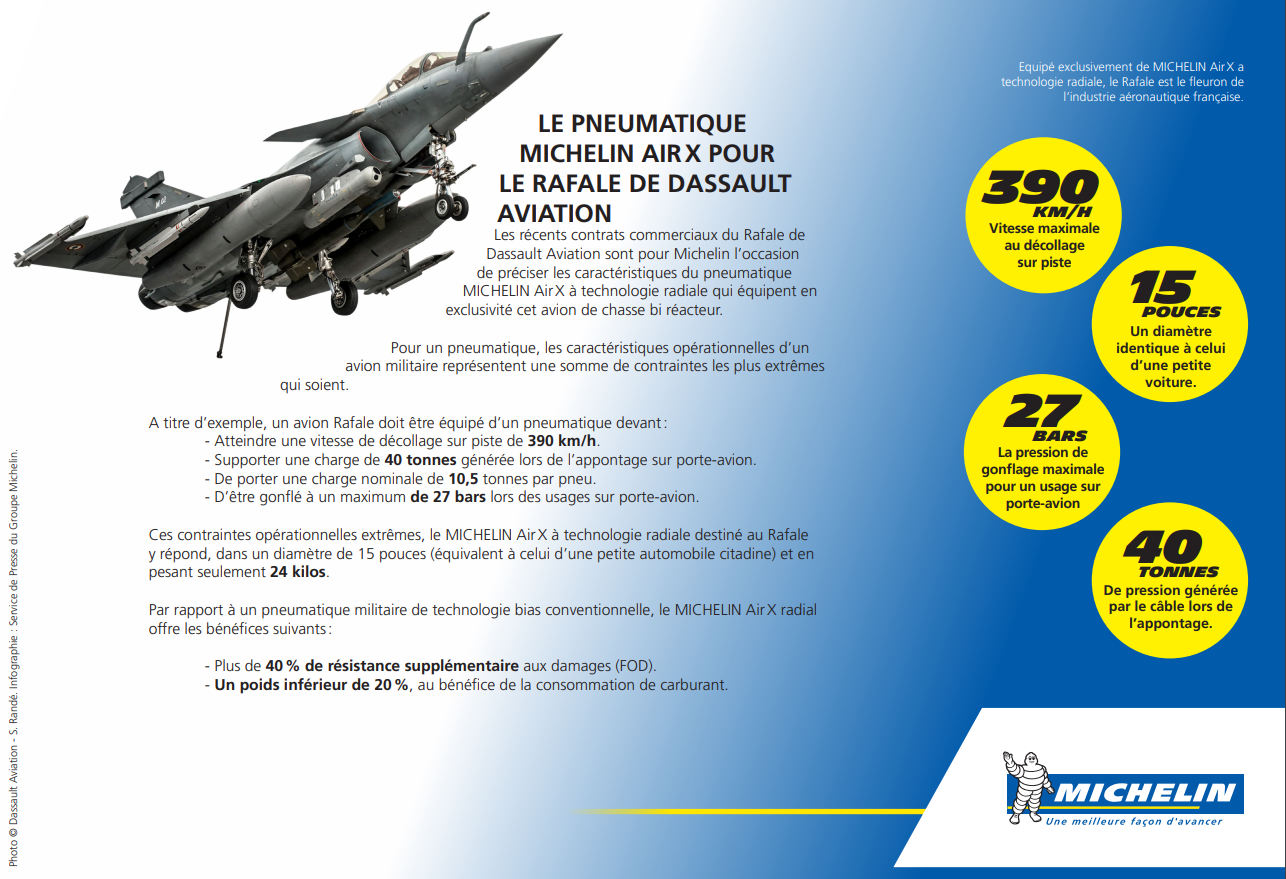
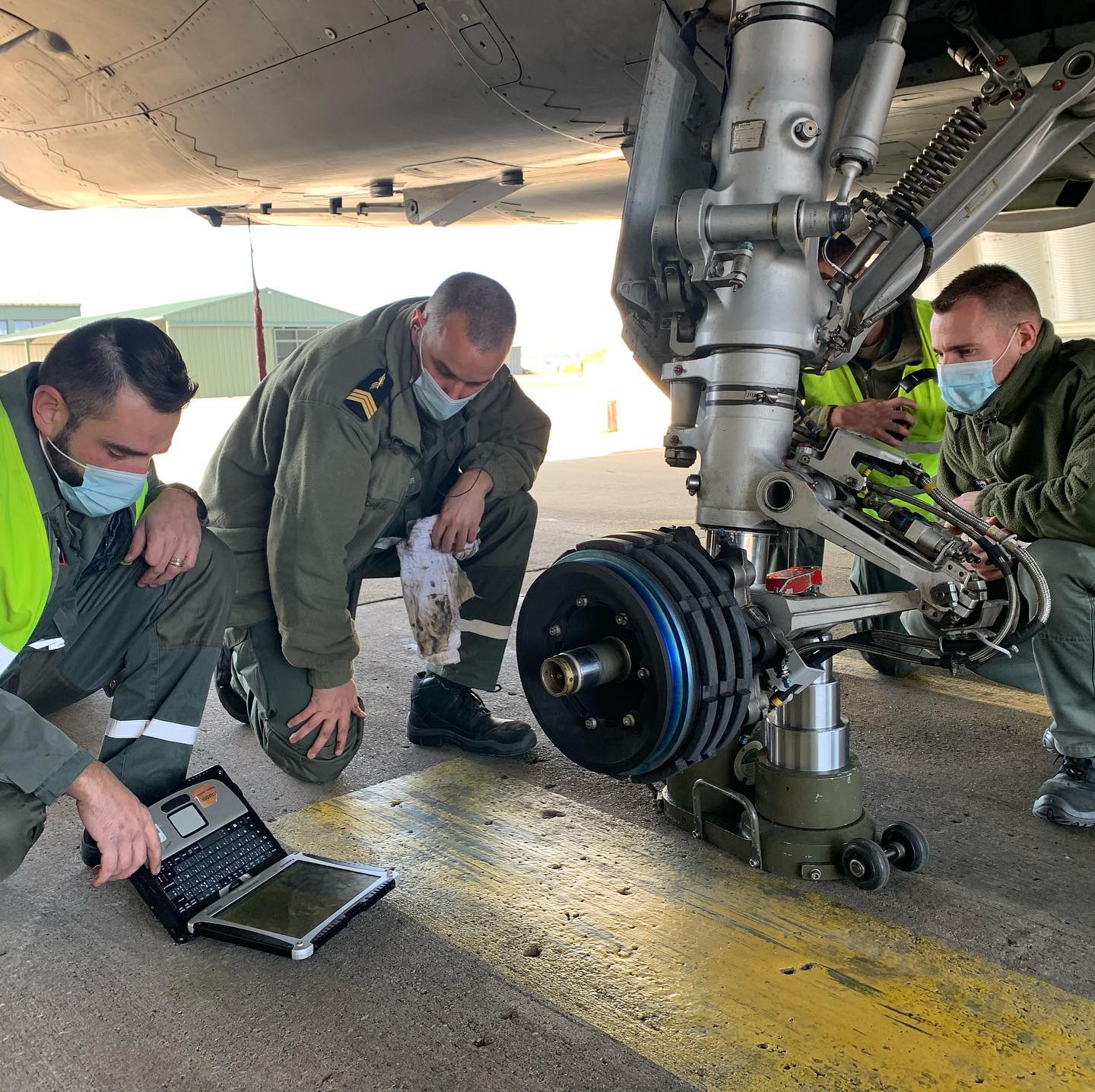
Les trappes de visites du Rafale

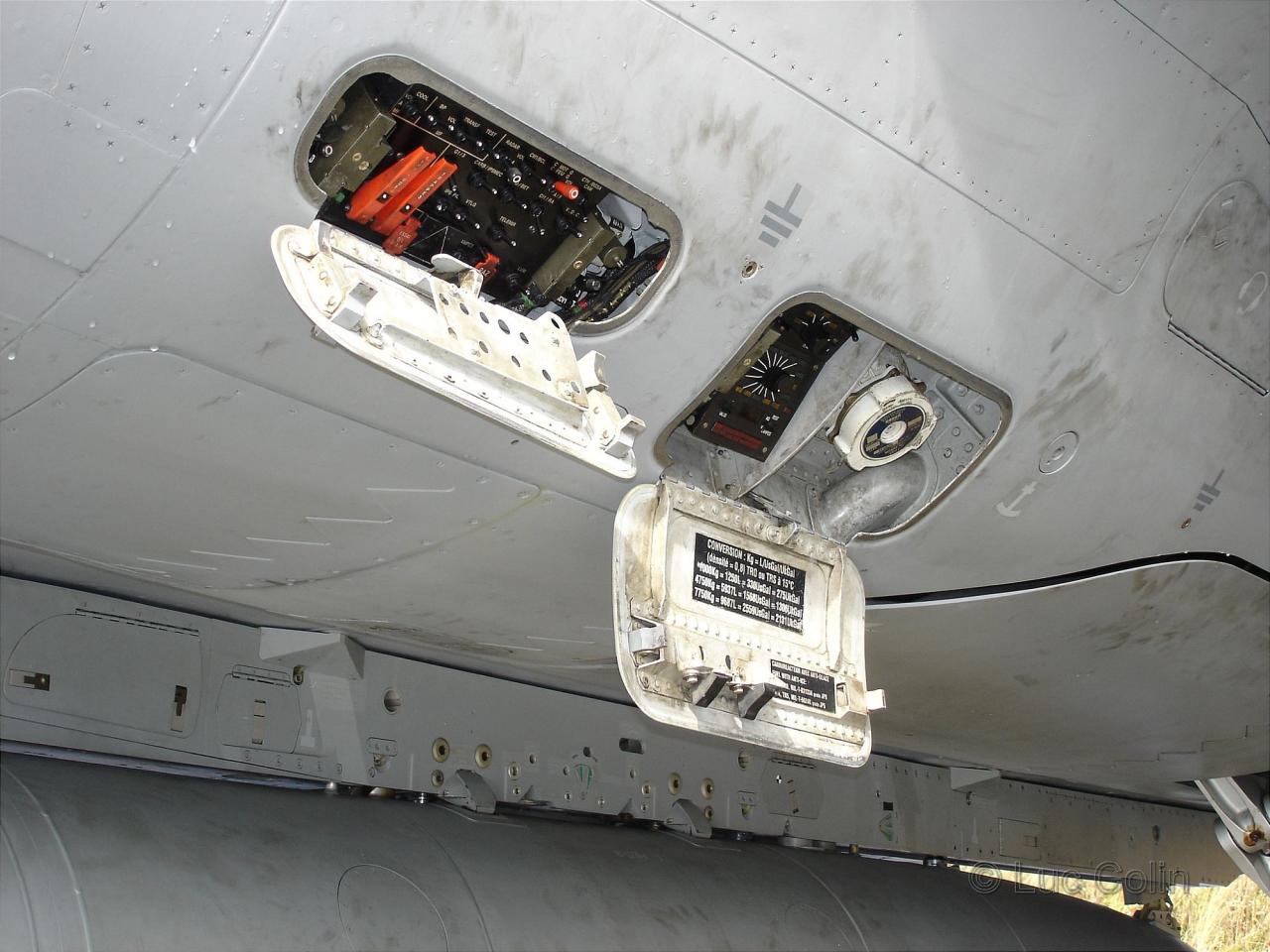

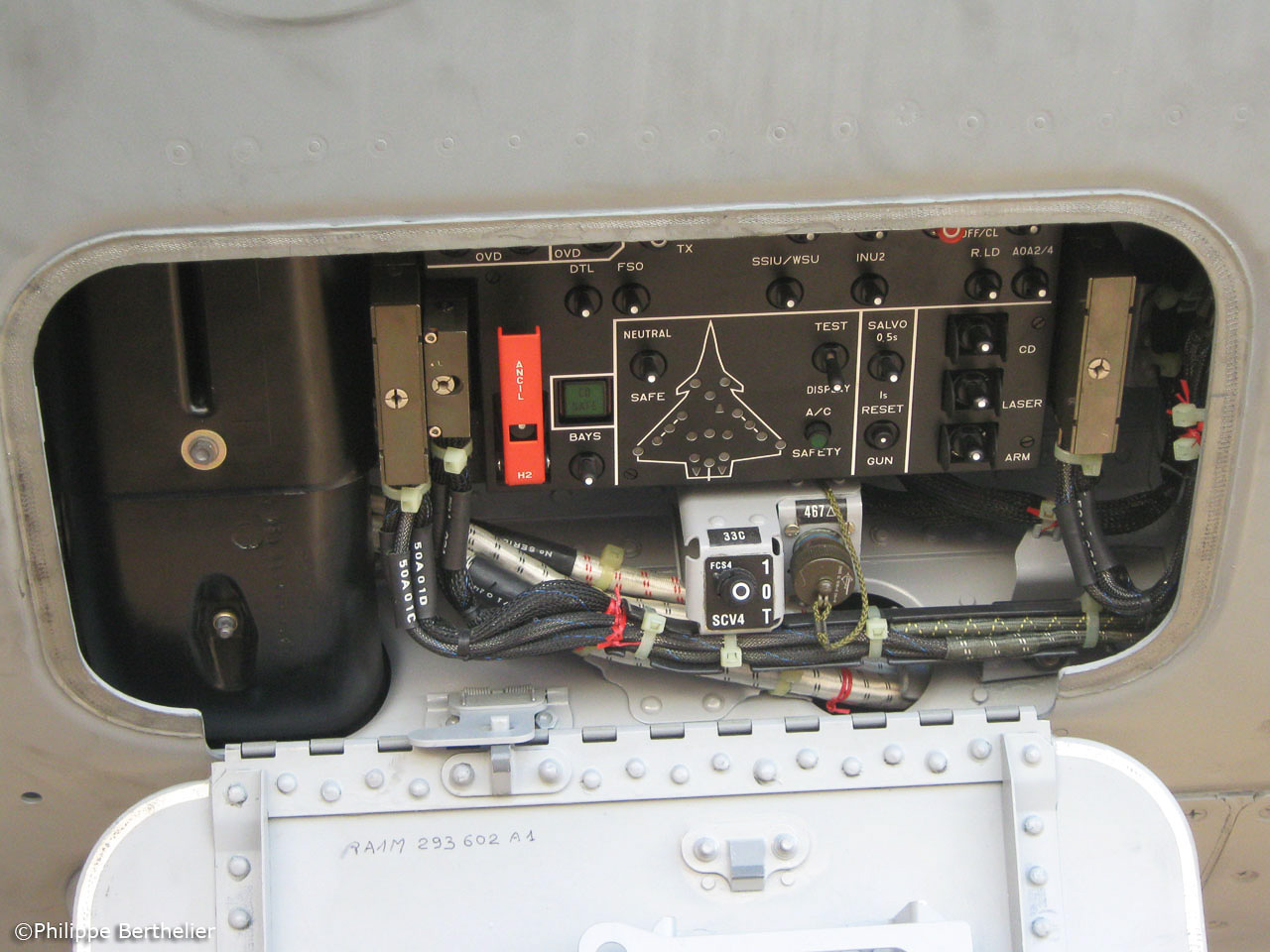

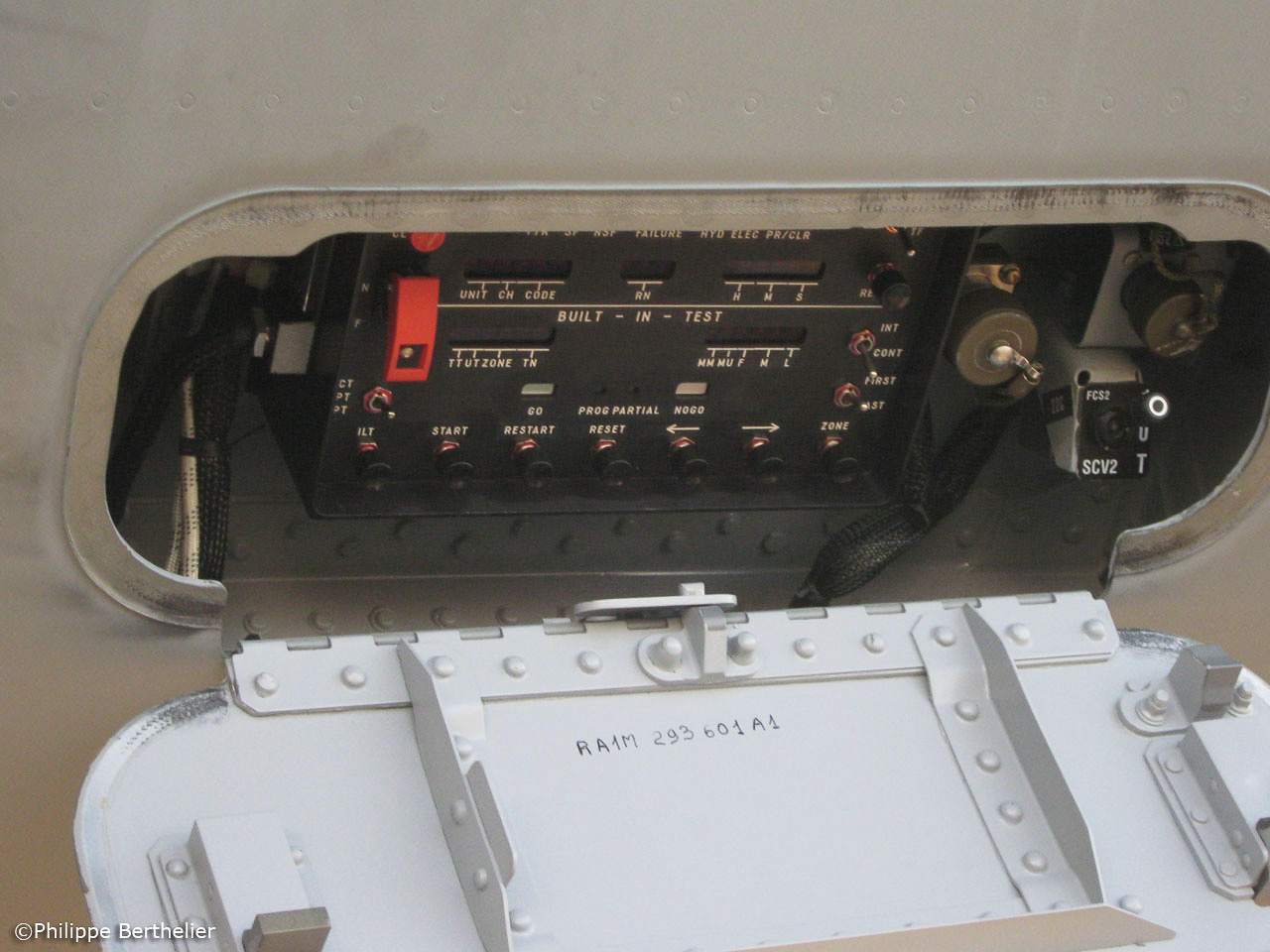

Le siège éjectable Martin Baker Mk-F16F
Il est incliné à 34° (19° sur le Typhoon) pour permettre au pilote une meilleure endurance face aux facteurs de charges. En outre, ce siège permet une éjection à vitesse et altitude nulles (zéro-zéro). Il pèse 90 kg et fonctionne jusqu’à 20000 m d’altitude pour une personne équipée pesant entre 63 et 106 kg.
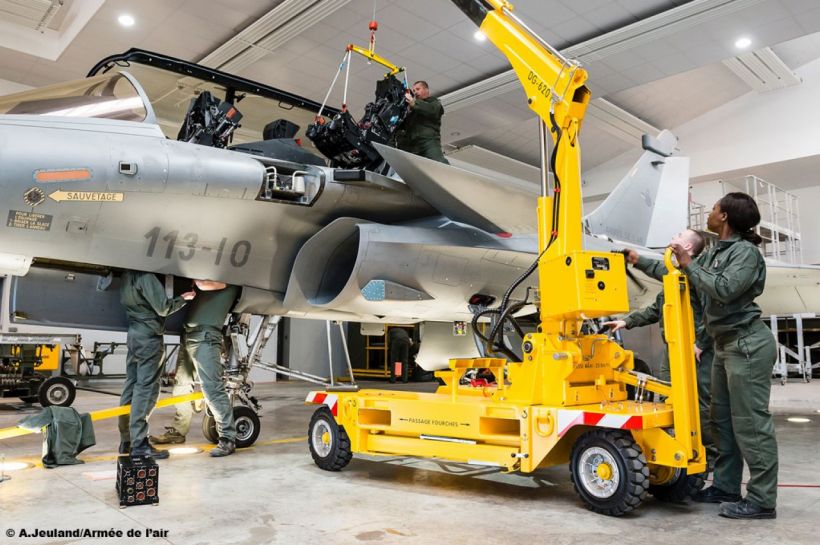
La vitesse d’éjection du siège est de 15m/s, l’avion pouvant évoluer jusqu’à 625 kts, soit 1125 km/h.
En 2021, Martin Baker revendique 7646 pilotes éjectés, dont 368 français et 3 pilotes de Rafale. Par ailleurs, le F-35, le Typhoon, le T-6 et le T-38 utilisent également une base de Mk-16.
Assis dans son cockpit, le pilote peut aligner 2 symboles situés à la base du HUD afin de régler parfaitement la hauteur du siège (le second symbole est spécifique au réglage en « mode appontage »). Le réglage est vertical, et non selon l’inclinaison du siège.
Lors de l’éjection, le siège part légèrement vers la gauche, en conséquence, sur la version biplace, le siège arrière part vers la droite. Ces trajectoires proviennent des Rafale M. En effet, en cas d’éjection à l’appontage, le pilote est ainsi écarté de l’îlot (superstructure du porte avions). De cette manière, pilote et passager arrière sont éjectés via des trajectoires opposées pour éviter une éventuelle collision.
Un cordon pyrotechnique au sommet de la verrière coupe celle-ci en deux afin de permettre le passage de l’équipage à travers. Deux plaques en composites (blanches) servent à ce que la partie arrière de la verrière parte lors de la fragilisation.
Séquence d’éjection
Sur la version biplace du Rafale, la séquence est la suivante :
- Si le pilote arrière déclenche celle-ci, son siège part immédiatement, puis le pilote avant est éjecté 0,5 seconde après.
- Dans le cas contraire, le pilote arrière est éjecté 0,17 seconde après l’ordre du pilote avant. Le siège avant le suit 0,33 secondes plus tard.
Au départ, l’accélération est de 15g et propulse les pilotes à 15 mètres de l’avion en altitude, et 50 mètres au niveau du sol.
Le déclenchement se fait uniquement par une poignée basse, et la verrière se brise par un système pyrotechnique. Cette fragilisation de la verrière permet aux morceaux de s’écarter du pilote par action du vent relatif. Enfin, en cas de non fonctionnement, le siège passe à travers de la verrière.
Contrairement au Mk-10 du Mirage 2000, le Mk-16 dispose de 2 canons pyrotechniques et diverses nouveautés :
- meilleur équilibrage du siège grâce à un parachute stabilisateur à 4 brins et 2 aérodynamiques (plaques métallique qui se déploient de chaque côté)
- ouverture dynamique du parachute (et non plus par vent relatif)
- rappels de jambes et bras par des sangles qui impose une surveste spécifique avec protection anti-g et dispositif de flottabilité.
Lors d’une éjection en haute altitude, le siège éjectable libère le pilote vers 2400 m d’altitude.
3000 pièces composent le siège éjectable
La maintenance de tous les sièges de l’armée de l’air s’opère entre la SEM MB et l’AIA d’Ambérieu, organisme du service industriel de l’aéronautique (SIAé), rattaché à l’armée de l’air depuis le 1er janvier 2008.
Par ailleurs, quelques 3 000 pièces composent le siège éjectable, dont Dassault fabrique la ligne pyrotechnique à Poitiers sous la responsabilité de SEM MB. Ce dispositif pyrotechnique à onde de choc permet une unicité de commande spécifique au siège MK16. En effet, lorsque le pilote tire la poignée d’éjection, il déclenche l’ensemble du processus d’éjection :
- mise en œuvre du rappel de harnais,
- initiation de la cartouche du canon d’éjection,
- fragilisation de la verrière
- mise en œuvre du système inter-sièges pour les avions biplaces.
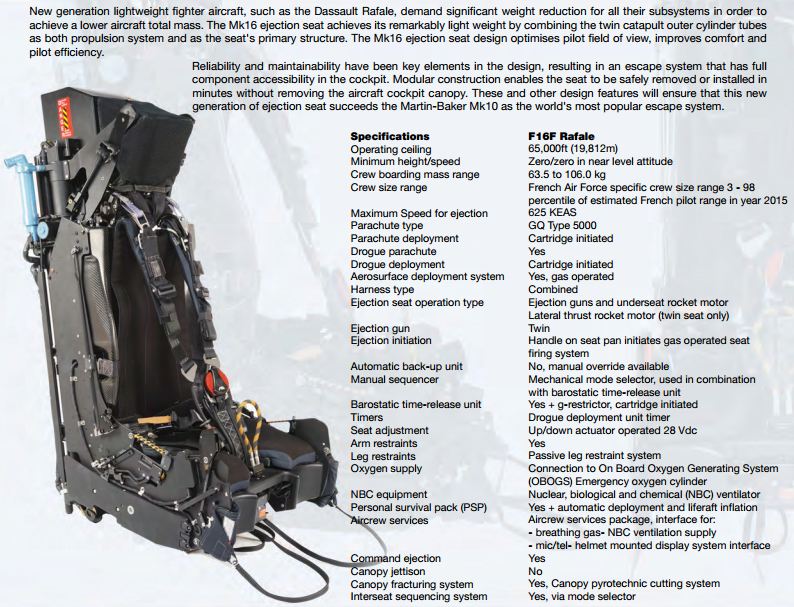
Un peu d’histoire
Dans les murs de la société d’exploitation des matériels Martin-Baker, en région parisienne, une histoire circule autour de la naissance des premiers sièges éjectables.
Lors de sa création en 1929, l’entreprise britannique se consacrait exclusivement à la fabrication d’avions. L’origine de son nom provient des deux associés : Sir James Martin, inventeur et ingénieur aéronautique, et le capitaine Valentine Baker, instructeur et pilote d’essais. La société a conçu et développé quatre modèles d’avions lors de la Seconde Guerre mondiale. Néanmoins, le peu de succès et les difficultés rencontrés à l’époque ont été fatals aux prototypes développés.
Les prototypes MB1, MB2, MB3 et MB5 ne virent jamais le jour comme appareil de série. C’est à la mort accidentelle du capitaine Baker, survenue lors d’un vol d’essais, que Sir Martin décide de se consacrer au développement d’un système de sauvetage pour les navigants. L’entreprise mit au point un siège éjectable testé pour la première fois, le 24 juillet 1946, sur un Gloster Meteor.
Aujourd’hui encore, les sièges des aéronefs de combat fonctionnent selon les mêmes principes de base. L’évolution des techniques a permis d’agrandir le domaine d’utilisation, avec des vitesses bien plus élevées. Il devient même possible de s’éjecter au niveau du sol tout en minimisant les dommages corporels.
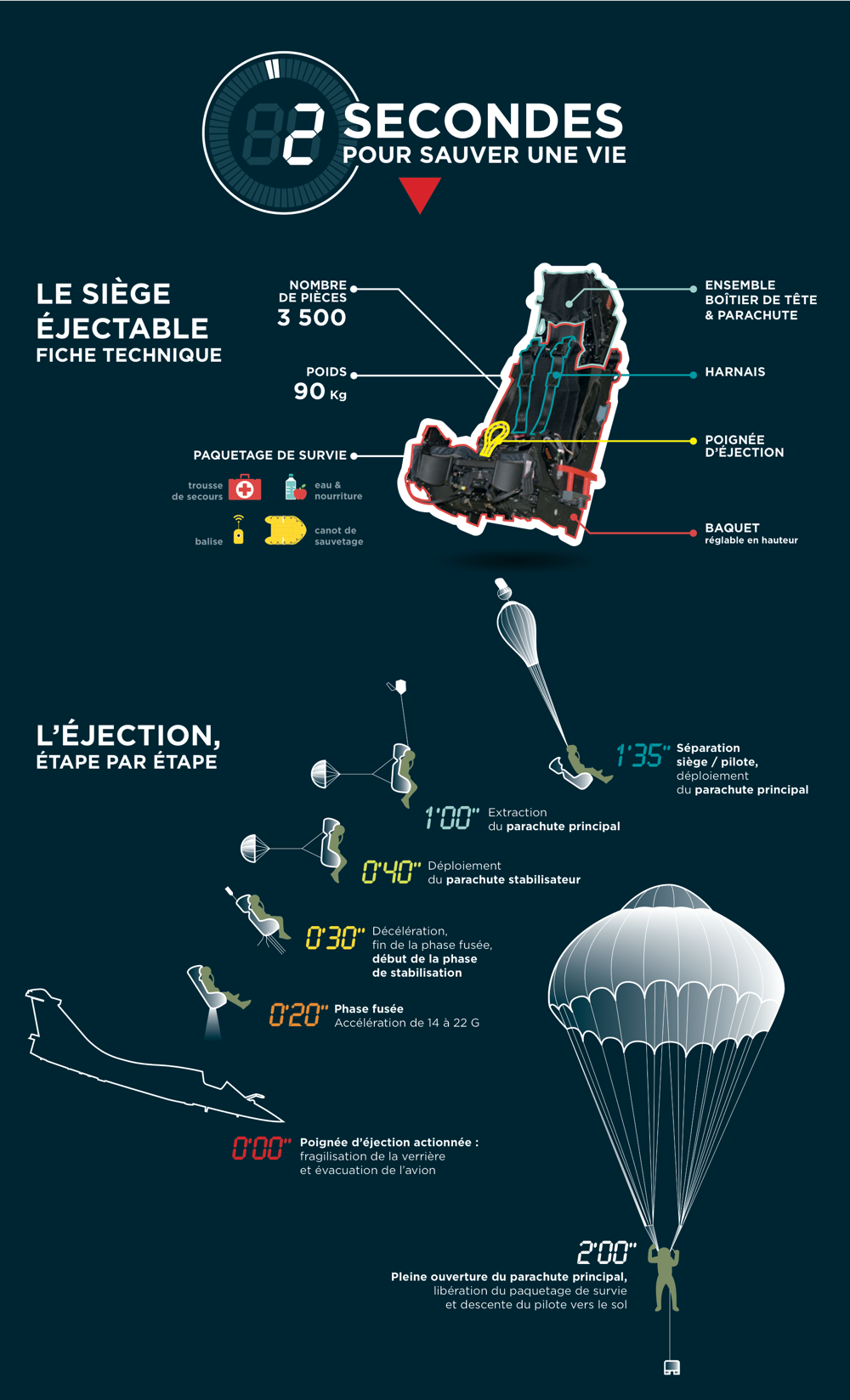
Source : Air Actualité n°638.
Début 2016, la Société d’exploitation des matériels Martin Baker produit le 250e siège éjectable MKF16F. Les sièges SEMMB ont sauvé la vie de 698 pilotes depuis le début de leur production en 1961. L’entreprise a fabriqué 5700 sièges, dont :
- 1470 pour le Mirage 2000,
- 47 pour le Super Etendard,
- 220 pour l’Alphajet.
Une verrière en 2 parties, contrairement au démonstrateur Rafale A
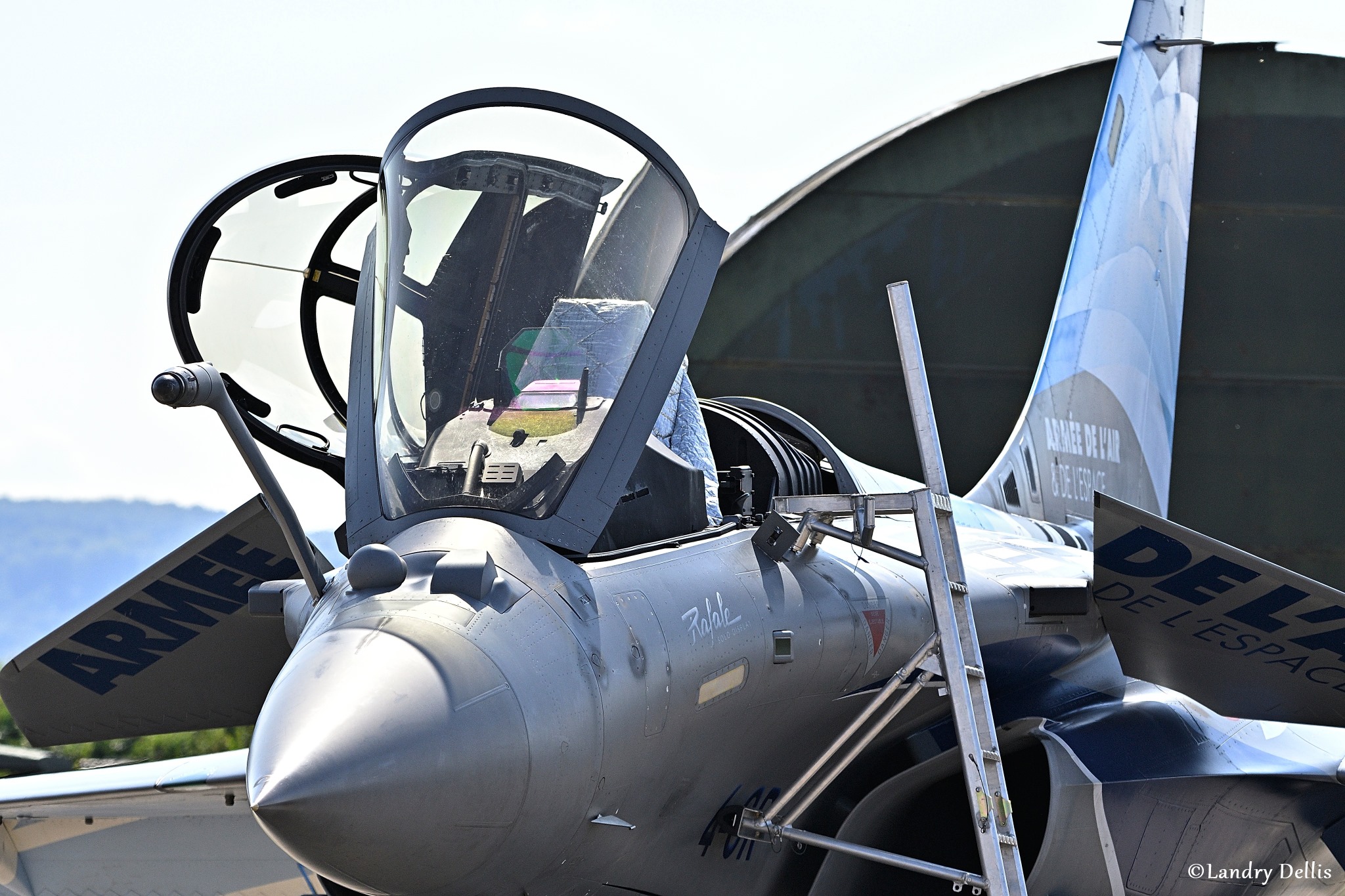
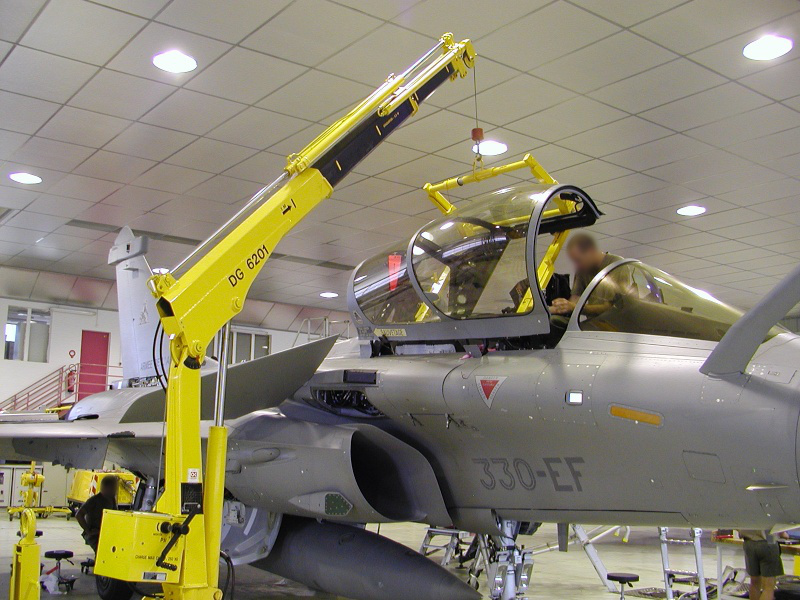
Un nouveau simulateur de siège éjectable
En avril 2021, la Base Aérienne 118 inaugure un nouveau simulateur de siège éjectable : SIE3RA (SImulateur d’Entraînement à l’Evacuation d’urgence et l’Ejection du RAfale. Entièrement en composite, le projet voit le jour en 2015, et permet une restitution physique des moindres détails de l’avion. Il permettra aux équipages de répéter tous les types de procédures auxquels ils pourront faire face :
- éjection au dessus d’une étendue d’eau
- feu qui se déclare au sol
- premiers geste à à la descente sous voile
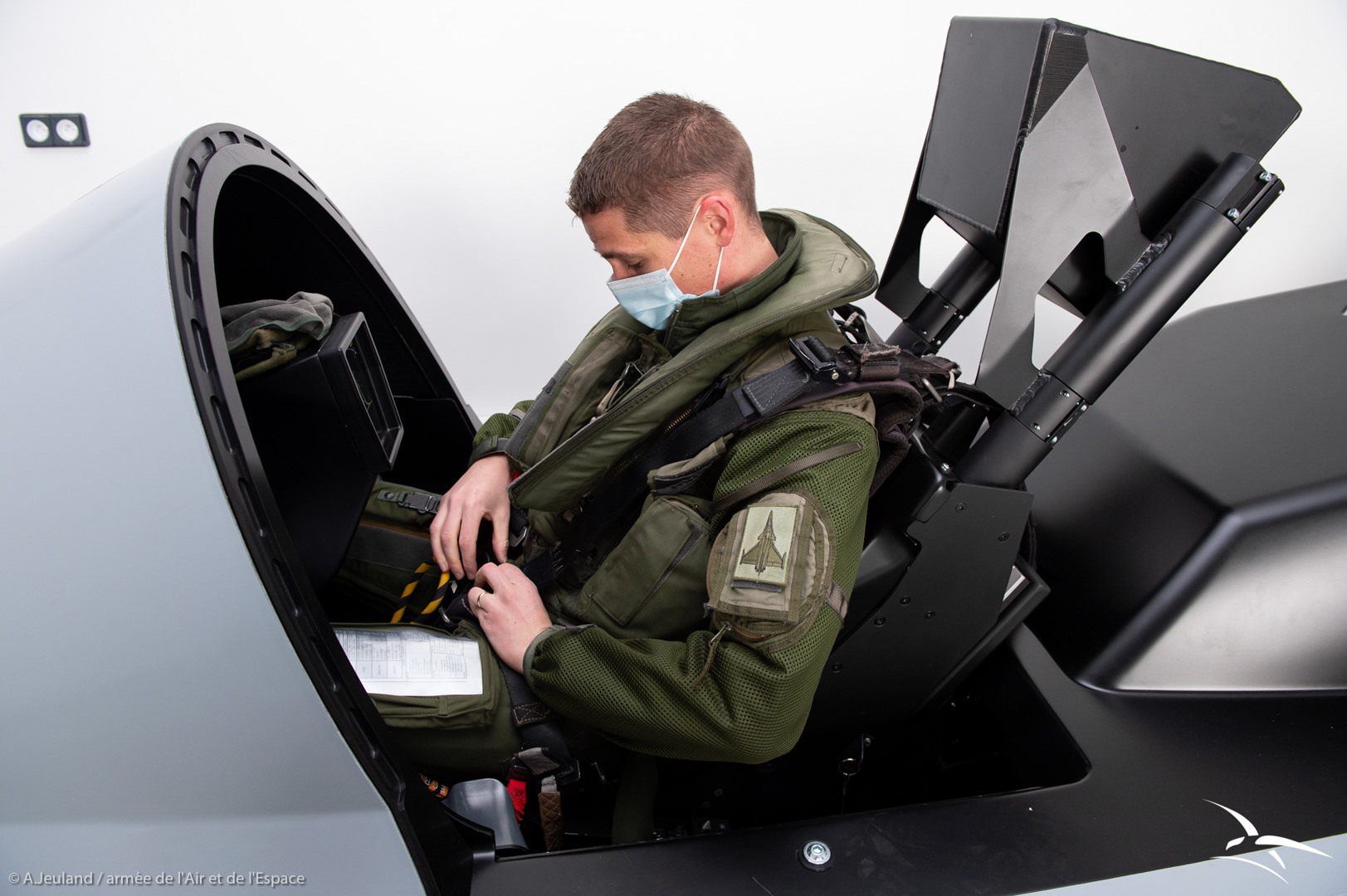
Antenne TELEMIR
Petite antenne visible au sommet de la dérive des Rafale M. Il s’agit là du système d’alignement à la mer : TELEMIR (Infra Rouge). A noter que, depuis 2015, cet appendice n’est plus fonctionnel. En effet, la transmission des informations nécessaires aux centrales inertielles et provenant du porte-avions ne s’effectue plus par infrarouge.
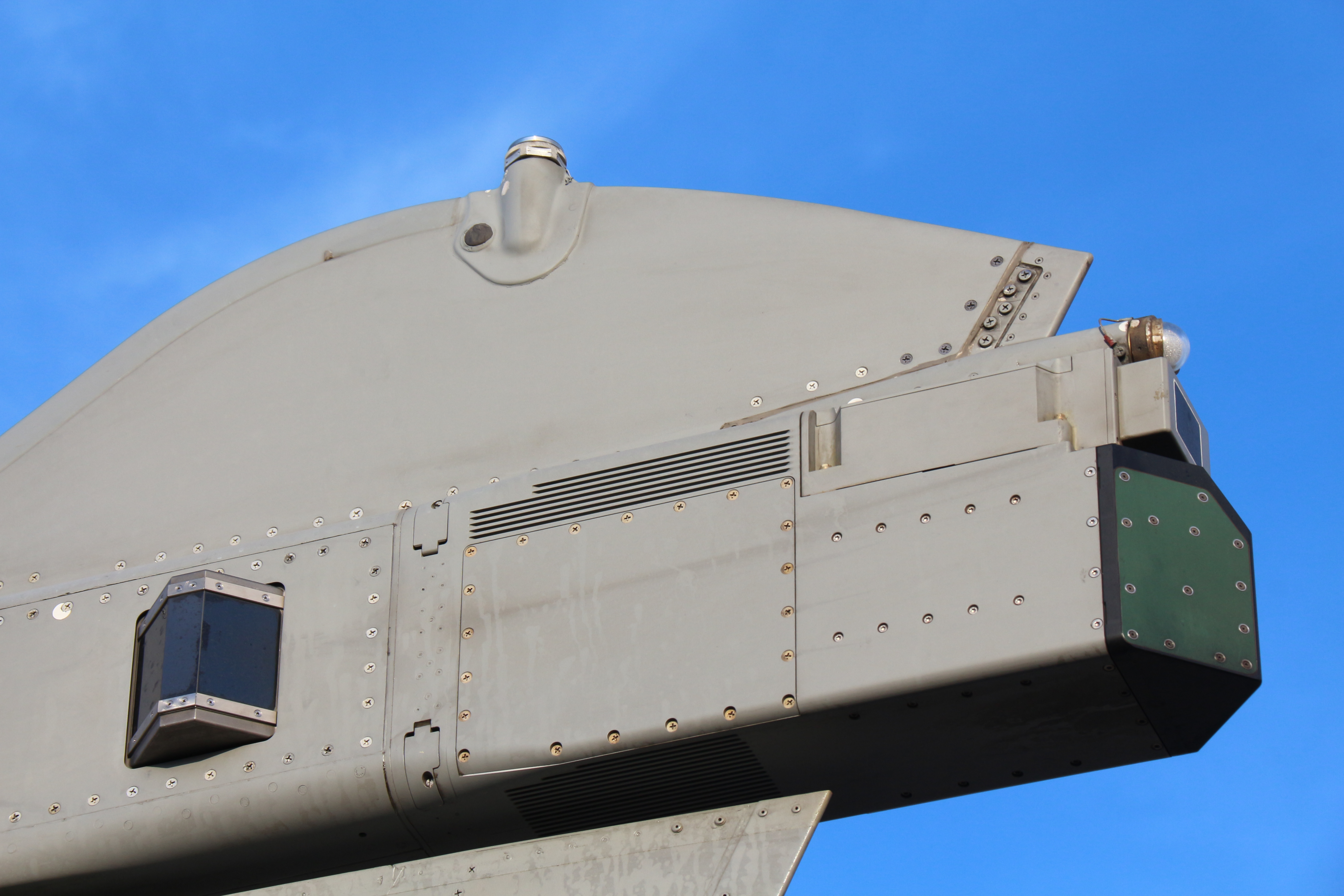
Mallettes de contrôle Système Télémir (SECA)
Ces mallettes permettent le contrôle, à bord du porte-avion Charles de Gaulle, des équipements de transmission Télémir embarqués et localisent d’éventuelles pannes. Le système infra-rouge Télémir permet au porte-avion la transmission d’informations à l’avion avant que celui-ci ne décolle.
Il se compose des éléments suivants :
- une boîtier de traitement,
- une tête optique,
- un cordon de liaison.
Caractéristiques principales:
- Alimentation monophasé 115Vac 400Hz ou 230Vac 50Hz, sur réseau atelier ou sur avion,
- Utilisation sur pont d’envol ou dans hangar,
- Température de fonctionnement -20 à +70°C,
- Température de stockage -30 à +70°C,
- Qualification GAM EG13-C.
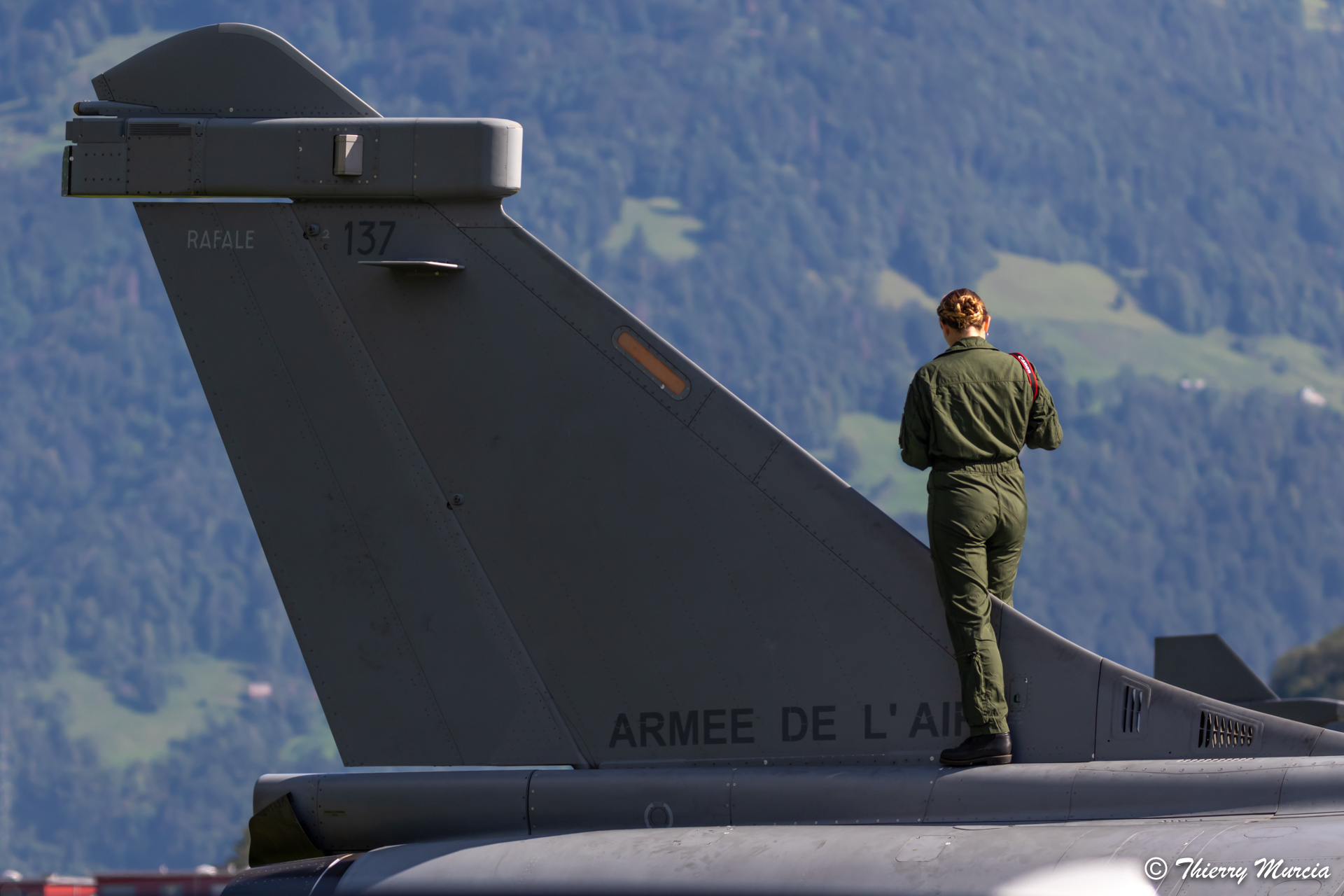
Visite guidée d’un Rafale B (Mont de Marsan – 2014) © Philippe AMIEL
Vous êtes ici : Accueil / Technologie (Menu) / Avionique / Walkaround